摘要:針對現(xiàn)有各流量計機械結(jié)構較復雜、低流與微流難以檢測的不足,一種基于差壓原理的一種新型差壓液體流量計,該流量計以特制的導管和差壓傳感器作為流量檢測元件,用STC12C5410AD作為微處理器.檢測元件將差壓信號轉(zhuǎn)換為電信號,該電信號經(jīng)儀表放大器放大后,用微處理器進行數(shù)據(jù)采集和處理,獲得流量和流速值.
0引言
流量的測量與控制在各個領域都非常重要并得到廣泛應用.現(xiàn)有的流量傳感器多種多樣,它們的原理有電磁[1,2]、超聲波[3,4]、渦輪[5]、光纖[6]、壓力等,超聲波式和渦輪式在各個領域得到普遍應用.然而,以上各種流量計由于機械或電氣等方面的原因?qū)π×髁亢臀⑿×髁亢茈y被檢測到,有些流量計機械結(jié)構方面比較復雜[7];有些不便于操作和實現(xiàn)自動控制[8].為了滿足變量噴霧機藥液流量檢測和控制的需要,提出了一種差壓式液體流量檢測方法[9].一種新型流量計,該流量計由特殊的導管、差壓傳感器、儀表放大電路、STC12C5410AD單片機和顯示按鍵電路等組成,該裝置與現(xiàn)有的流量計比較有以下的優(yōu)點:1結(jié)構簡單,2量程寬,3性能較穩(wěn)定,4誤差在±1%以內(nèi).
1流量檢測元件設計
差壓式液體流量傳感器的結(jié)構如圖1所示,主要由導液管和差壓式壓力傳感器組成.26PC差壓式壓力傳感器.導液管由輸入管、節(jié)流管、輸出管和兩個取壓管組成,兩個取壓管由輸入管和輸出管引出,用于把連接差壓傳感器,以便差壓傳感器檢測出這兩點的壓力差.
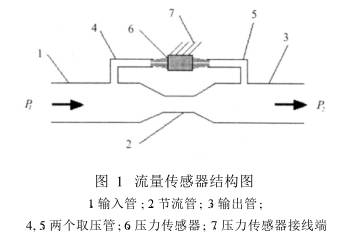
輸入管和輸出管的內(nèi)徑比節(jié)流管大,取壓管的內(nèi)徑通常較小.如圖1所示,輸入管、節(jié)流管和輸出管被連接成“一”字型,取壓管被對稱地接在輸入管與輸出管上.差壓式壓力傳感器,通過氣管被連在兩取壓管上.當有液體流過導液管時,輸入管與輸出管之間會產(chǎn)生的壓力差,輸入管壓力大于輸出管的壓力,由差壓式傳感器檢測這兩端的壓力差,并轉(zhuǎn)換成電壓信號.
文丘里管主要差別是低壓端取壓管不是從節(jié)流管引出,而是由輸出管引出,所以產(chǎn)生差壓的原理完全不同.文丘里管的壓力差是由兩個取壓點的流速差獲得,可以用來測量理想流體的流速,而本差壓流量計的差壓是由管道沿程損失和局部損失產(chǎn)生.現(xiàn)有流量計象渦輪式、超聲波式,電磁式流量計會受到尺寸太小限制,國內(nèi)低流與微式流量計暫時沒有.差壓流量計的管道內(nèi)沒有任何阻件,節(jié)流管內(nèi)徑可大可小,這是優(yōu)于其它流量計之處,節(jié)流管內(nèi)徑越小,設計出的流量范圍就越小,推出了流量為0.1ml/s以下的流量計.壓力差大小與通過導液管的單位時間內(nèi)液體流量(流速)有確定的關系,其關系可由以下等式來表達[10]

式中,Qv為單位時間的體積流量,T為流量計的轉(zhuǎn)換系數(shù),Y為流體澎脹率,對于液體Y=1,g為當?shù)刂亓铀俣?P1-P2為輸入管與輸出管之間的壓力差,d為流體密度.等式(1)為用體積流量來表示,也可轉(zhuǎn)換為質(zhì)量流量表示,如式(2)

式中,Qm差壓流量計的質(zhì)量流量,其常與(1)相同從等式(1)和(2)可以清楚地看到當T,Y,g和d不變時,流量與壓力差的平方根成正比.流量轉(zhuǎn)換系數(shù)T是很復雜的一個常數(shù),它決定于傳感器的結(jié)構和方法,比如與獲取壓力的方式和位置等因素有關.
2軟硬件設計
流量檢測元件中的差壓傳感器將所檢測到的差壓轉(zhuǎn)換成電信,并經(jīng)后續(xù)電路放大,再送單片機進行AD采集和處理.
2.1硬件電路設計
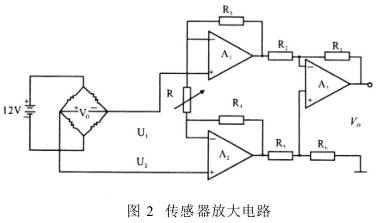
壓力檢測傳感器采用26PC系列差壓傳感器,其內(nèi)部電路為直流電橋,電橋用12V電源供電,其輸出端接儀表放大電路,如圖2所示.此電路所輸出的電壓與傳感器所受到的差壓成線線關系[9],即Vo∝(P1-P2),因此有

式中,k為壓力差與輸出電壓之間的轉(zhuǎn)換系數(shù),由式(3)可見,液體的體積流量(質(zhì)量流量或流速)與檢測電路所輸出的電壓的平方根成正比,只要AD轉(zhuǎn)換器對電壓進行采集,便可換算成流量.本系統(tǒng)中,采用STC12C5410AD單片機進行數(shù)據(jù)處理,此芯片內(nèi)部自帶八路10位ADC模數(shù)轉(zhuǎn)換電路,當采用22M晶振時,采樣時間僅為10μs,能滿足設計要求.
2.2軟件設計
流量計的數(shù)據(jù)采集、數(shù)據(jù)處理和數(shù)據(jù)顯示主要單片機的軟件是完成的關鍵,首先將儀表放大電路輸出的電壓送單片機進行AD數(shù)據(jù)采集,將采樣結(jié)果進行轉(zhuǎn)換,將電壓值轉(zhuǎn)成流量值,然后送顯示器進行顯示.其工作流程如圖3所示.
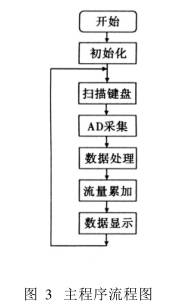
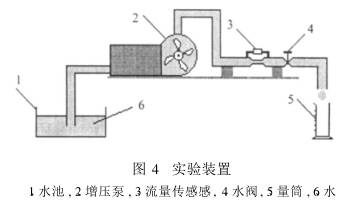
3實驗標定與結(jié)果
3.1實驗裝置
為了證實所提出的方法的可行性,完成了大量的實驗,并對傳感器進行了標定.實驗裝置主要由被標定的流量計、增壓泵、水閥、量筒和水池等組成,如圖4所示.為了簡化實驗過程,把水當作測試樣品.
在實驗系統(tǒng)中,導液管輸入管和輸出管內(nèi)徑為3.6mm,節(jié)流管內(nèi)徑為1.4mm,節(jié)流管長54cm,兩個取壓管內(nèi)徑為1.4mm;壓力傳感器采用了26PCBFA6D型,放大電路放大倍數(shù)約為37dB;單片機控制系統(tǒng)采用了STC12C5410AD作為微處理器.單片機控制器主要有計時、電壓采樣、流量處理、流量累計和顯示等功能.
3.2標定實驗及數(shù)據(jù)處理
在水溫為25℃的條件下進行了標定實驗.當水流過導液管時,固定流速不變,用單片機記錄時間、采集放大電路輸出的電壓,同時用量筒測量這一時間內(nèi)流過水的體積.調(diào)節(jié)水閥改變流速,重復操作,得出一電壓隨流速變化的一組實驗數(shù)據(jù).由量筒所測得的水的體積和單片機所記錄的時間,可以計算出不的體積流量,以體積流量作為橫坐標,單片機AD采集所獲得的數(shù)值作為縱坐標,并經(jīng)曲線擬合,可以得到圖5.其擬合曲線公式為
Vo=4.2729Q2v+9.6063Qv+8.5132,
由式(4)可知,電壓是流量的二次曲線.將電壓的平方根與流量進行曲線擬合可得到圖6示曲線,其關系可表達為
上式經(jīng)變形可得到式(6)
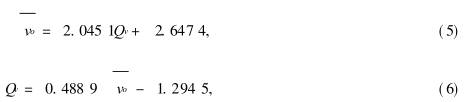
式(6)與式(3)相比,除多一個常量外,形式基本上是一致的,也就證明了所設計流量計理上是正確的.
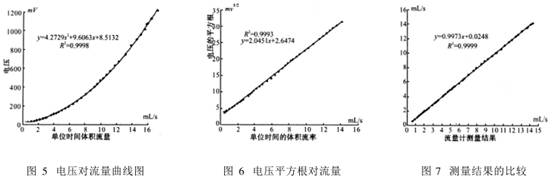
由等式(6)可知,只要用單片機采集電壓值,就可以換算得到液體的流量值.將公式(6)入程序后,用此流量計進行了流量測試,流量計測量結(jié)果和實際流量數(shù)據(jù)所圖7所示.
圖7中的實驗數(shù)據(jù)表明,流量計測得數(shù)據(jù)和實際測得的數(shù)據(jù)從1mL/s到15ml/的范圍里基本上成一條直線,在以上量程范圍里最大誤差不超過±1%.
4結(jié)論
一種新型差壓式液體流量計,由于節(jié)流管內(nèi)部沒有任何阻件,內(nèi)徑大小不受限制,所以能設計的流量范圍寬.在25℃溫度時,流量計以水作為工作流體進行實驗標定和實際測試,結(jié)果發(fā)現(xiàn)實驗數(shù)據(jù)與理論推算吻合,誤差在±1%以內(nèi),能夠滿足變量噴霧機藥液檢測的要求.然而,流量會受溫度的影響,溫度補償問題有待進一步研究.
以上內(nèi)容源于網(wǎng)絡,如有侵權聯(lián)系即刪除!