摘要:通過CFD流體軟件對內錐流量計壓力損失進行了數值模擬,實驗介質為汽油與柴油的混合物。內錐流量計和孔板流量計經常使用于流體計量,在保證兩種流量計流通面積相等的條件下,對它們的壓力損失進行了比較。結果表明,內錐流量計的壓力損失僅為孔板流量計壓力損失的30%左右,將內錐流量計應用于流體計量,可以起到節(jié)能降耗的作用。
0引言
在許多情況下,由壓力損失所引起的額外的耗能費用是選用流量計時必須要考慮的一個重要因素。流量儀表的壓力損失小已經是選擇流量計的一項重要指標。由于內錐流量計和孔板流量計使用的條件相似,并且使用廣泛,因此有必要對這兩種流量計進行壓力損失比較,以便選出更合適的測量儀表。雖然人們對內錐流量計和孔板流量計的壓力損失進行過比較,但目前文獻[1-2]中所作的比較存在兩個問題。第一,文獻中多是通過比較兩種流量計的壓力損失計算公式來對兩種儀表進行比較。
對于孔板流量計,它的歷史較長,有統(tǒng)一的國際標準,可以直接算出壓力損失。對于內錐流量計,它的歷史相對較短,沒有統(tǒng)一的國際標準,給出的一些計算公式也不太成熟,通常計算值與真實值之間存在較大的誤差。例如,內錐流量計的生產廠家即使是按照行業(yè)規(guī)范生產的同一型號的內錐流量計,其給出的計算內錐流量計的壓力損失系數也是各不相同的,這就給用公式計算壓力損失帶來了誤差。第二,對兩種流量計壓力損失比較時,并沒有規(guī)定兩種流量計的有效流通面積相同,所得到的結果缺乏說服力。基于以上兩個原因,本文用CFD數值模擬的方法,計算出內錐流量計的壓力損失,并在保證有效流通面積的條件下對兩種流量計的壓力損失進行了比較,并且對兩種流量計進行了經濟技術分析,對選用流量計及計算內錐流量計的能耗都有很好的參考價值。
1模型建立
1.1幾何模型和湍流模型的建立
建立長L=14m,內徑D=0.2m的管道模型,模擬了前錐角為45°,后錐角為120°的V錐體壓力分布情況。
由于內錐體為旋轉體,具有軸對稱特性,在進行數值模擬實驗時,所建立的模型為二維結構,并進行了簡化處理(計算域選取一半),如圖1所示。
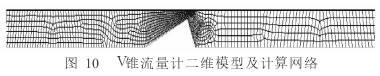
在網格的剖分方面,采用了結構化網格[3-4],如大比率四邊形網格計算長管形狀流場,網格數量明顯減少,在靠近錐體部分的網格進行加密設置,越靠近管道兩端,網格越稀疏。這樣做的目的是為了保持網格的光滑度,從而加速迭代收斂速度,避免因臨近單元體積或面積的快速變化而導致大的截斷誤差,節(jié)省計算時間。另外,在相同網格數量下,為更好保證計算精度,對流場影響最重要的部分進行了更精密的網格剖分。圖1即是采用此方法進行的網格剖分。
利用RNGκ-ε[5]模型進行計算,經物理實驗驗證顯示出了較好的預測性。另外,在近壁面區(qū)域采用標準壁面函數法進行處理。利用有限體積法實現(xiàn)控制方程的離散化,在求解離散方程過程中,采用以壓力為基本求解變量的求解方法,即SIMPLE算法進行求解。差分格式采用二階迎風格式。
1.2邊界條件和工作流體物性
邊界條件包括壁面、對稱軸、速度入口和壓力出口。流體從速度入口進入,流經節(jié)流裝置,最后由壓力出口流出。
內錐流量計的數值模擬實驗介質為柴油與汽油的混合物,其物理性質見表1所示。
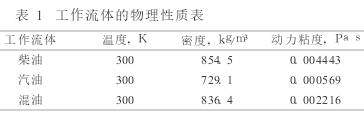
2內錐流量計的壓力損失模擬實驗
傳統(tǒng)測量孔板流量計壓力損失的方法[6]如圖2所示,分別測出、兩點之間的靜壓力,所得差值即為孔板壓力損失。為了使模擬的壓力是不可恢復性壓力,P1、P2兩點之間的距離應盡量遠,在本模擬實驗中管道直徑D=0.2m,P1、P2兩點之間的距離取50D,即兩個測壓點相距10m遠,模擬結果如表2所示。
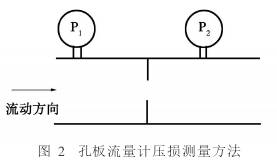
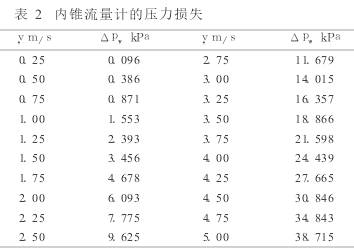
3內錐流量計與孔板流量計壓力損失比較
對于孔板流量計的壓力損失,用(ISO5167-2:2003)給出的計算公式進行計算,計算結果與內錐流量計壓力損失的模擬實驗結果進行比較。為了更好地對內錐流量計的壓力損失與孔板的壓力損失進行比較,選擇了有效流通面積相同的內錐流量計和孔板流量計進行比較,這樣的比較才有意義[7]。
內錐流量計錐體最大截面圓的直徑是dv=0.152m,流量計的直徑D=0.2m,管道截面面積Sc=0.031m2,有效流通面積為Sv=0.013m2。將內錐流量計的有效流通面積轉換為孔的面積,則對應的有效孔徑βv比為

取孔板流量計與內錐流量計有效孔徑比最接近的值βo=0.65。根據Reader-Harris[8]給出的流出系數的計算公式,求得平均流出系數C=0.61。在2003年實施的孔板流量計的國際標準(ISO5167-2:2003)中,壓力損失系數的計算公式為

將βo=0.65,C=0.61代人式(2),可以得到K=13.37
計算壓力損失Δpo的公式為

將流體密度ρ=836.4kg/m3與K=13.37代人式(3)可以得到

圖3反映了由式(4)計算出的在不同流速下孔板流量計的壓力損失曲線和內錐流量計壓力損失的實驗結果。
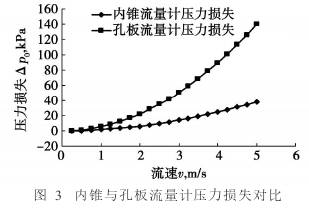
從圖3可以看出,在流通面積一定的情況下,孔板的壓力損失要大于內錐流量計,并且隨著流速的增加而增加。表3列出了在不同流速下,孔板流量計與內錐流量計的壓力損失,其中n為孔板流量計與內錐流量計壓力損失的比值。

4內錐流量計與孔板流量計能耗的比較
4.1計算動力與能量消耗和年耗能費
對于液體,可采用以下的計算公式[9]
P′=Δp·v·S/η
式中P′———所需要的功率,kW;
Δp———壓損損失,kPa;
v———工況下的流體的速度,m/s;
S———管道的橫截面積,m2。
計算年耗能費
Co=P′。t·X
式中Co———年耗能費,元;
t———運行時間,h;
X———電價,元/kW。h。
由于孔板前后都有大旋渦,在大幅值脈動壓力的背景噪聲條件下,只能通過縮小孔徑,提高差壓上限值來實現(xiàn)有效的流量測量。因此孔板的壓力損失必然增大。
由于內錐流量計測量壓差的背景噪聲小,可以檢測出較小的壓差,因此內錐流量計的壓損必然比孔板的壓損小,年耗能費也小。
4.2舉例分析
提到的內錐流量計與孔板流量計為例,工業(yè)電價為1元/kW·h,做出它們的年耗能費比較圖,如圖4所示。
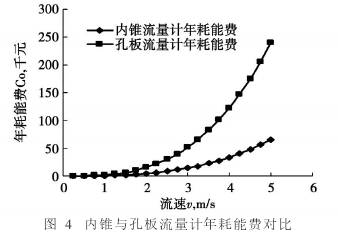
從圖中可以得到,隨著流速的增加內錐與孔板流量計年耗能費也逐漸增大,而孔板流量計的年耗能費要大于內錐流量計的年耗能費。這是因為內錐流量計的壓力損失比孔板的壓力損失小得多,年耗能費用可大大減少。流量計口徑越大,流速越大,則內錐流量計節(jié)能效果越顯著,投資回收期也就越短。
圖5表示的是內錐流量計相對比孔板流量計可以節(jié)約的年耗能費用,隨著流速的增大,節(jié)約的費用也就越多。
以流速v=5m/s為例,內錐流量計的年節(jié)約耗能為17411.9元,節(jié)能效果是非?捎^的。
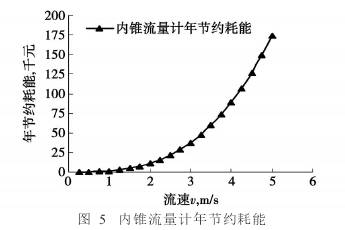
5結論
通過CFD數值模擬的方法,模擬了成品油管道中內錐流量計的壓力損失,同時與孔板流量計比較,得到了如下結論:
(1)內錐流量計的壓力損失比孔板流量計小,如果保證兩種流量計的有效流通面積相同,那么內錐流量計的壓力損失是孔板流量計的三分之一還要小一些。
(2)通過技術經濟分析可以明顯地看出:內錐流量計相比與孔板流量計,可以節(jié)約很多的能耗,符合國家的節(jié)能減排長期發(fā)展方針政策。
以上內容來源于網絡,如有侵權請聯(lián)系即刪除!